Business Talk: Pigeon-hole system for day-to-day stock control in your garage🕊️
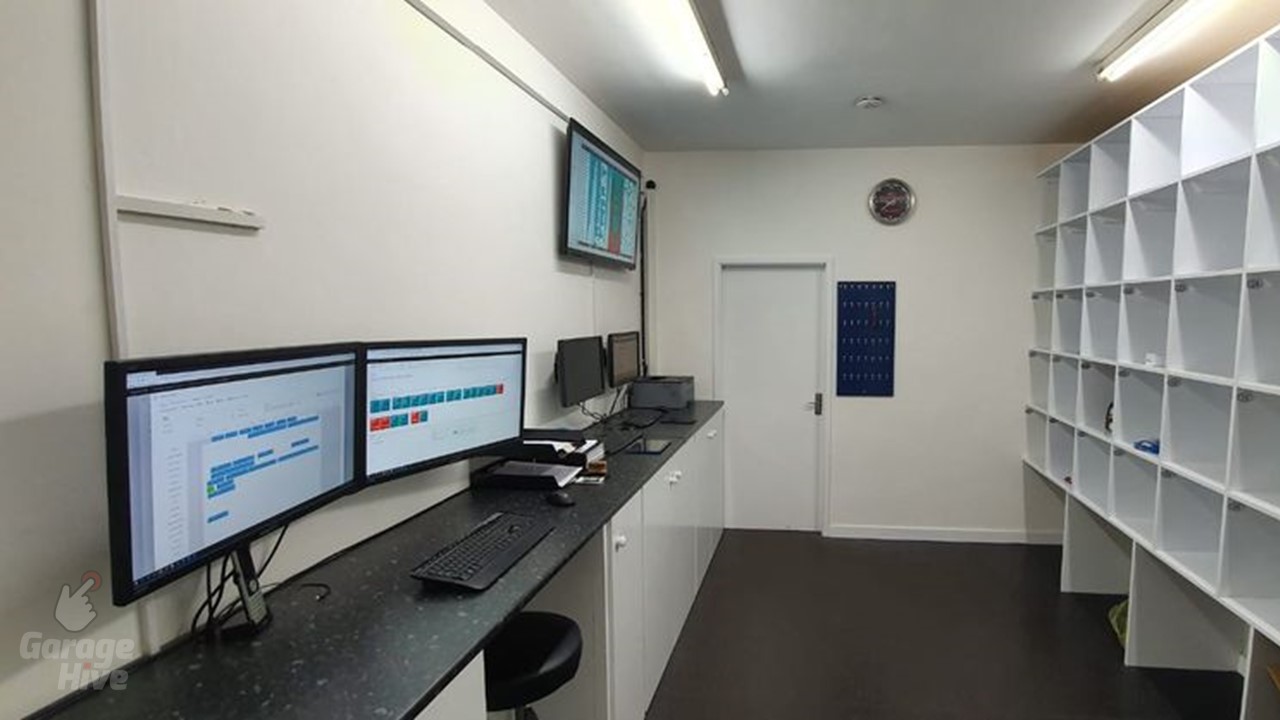
Are you struggling with vehicle parts management in your garage business, or do you think your technicians could be more efficient? We have a good tip from the industry best practice to help you out with this.
The Garage Hive team have visited many medium and small garages across the country over the years. Our implementation team have noticed certain trends of industry best practise that allows garages to function a lot smoother. An important one of these is the day-to-day parts organisation system. Regulating incoming stock is vital in avoiding time-wasting situations for your technicians.
A very convenient way to systemise vehicle parts and technician work allocation is known as the pigeon-hole system. (Special thanks to Mark Kettle at EAC Telford where the team first saw this)
First, let us look at a few examples of why there might be inefficiencies in the workflow:
- Confusing Administration: Your incoming stock is not being organised when entering the building, leading to confusion when trying to identify what is new or old stock. This leads to problems when finding the correct parts for jobs that are in the workshop, invoicing and subsequent returns and bookkeeping/accounting issues further down the line.
- Time Stealer: Your technician starts a job and halfway through realises that they do not have a part which they need. This leads to the technician having to leave the workshop to find the correct parts, which cost them time. The worst-case scenario is that due to unorganised stock, the part which is needed has not even arrived yet. The overall impact is a decrease in technician productivity and workshop efficiency, and the overall inconvenience reduces job satisfaction for the technician.
- Disrupted Workflow: Lack of synchronisation between the vehicle, the technician assigned to the job and the parts which are needed leads to inefficient operations within the workshop. As we all know, time is money; and time not spent on the job is wasted.
To tackle these struggles, we must start at the beginning. Incoming jobs that need to be assigned to technicians should be quick and easy to find, meaning technicians’ attention is only on the job at hand. It is an excellent practice to implement a referencing system. This ensures that the vehicle’s keys, parts needed for the job and the assigned technician are all efficiently organised. To do this, we suggest that you use key-tags with numbers (letters/symbols), a corresponding key-board or key-cabinet and numerical shelving or pigeon-holes.
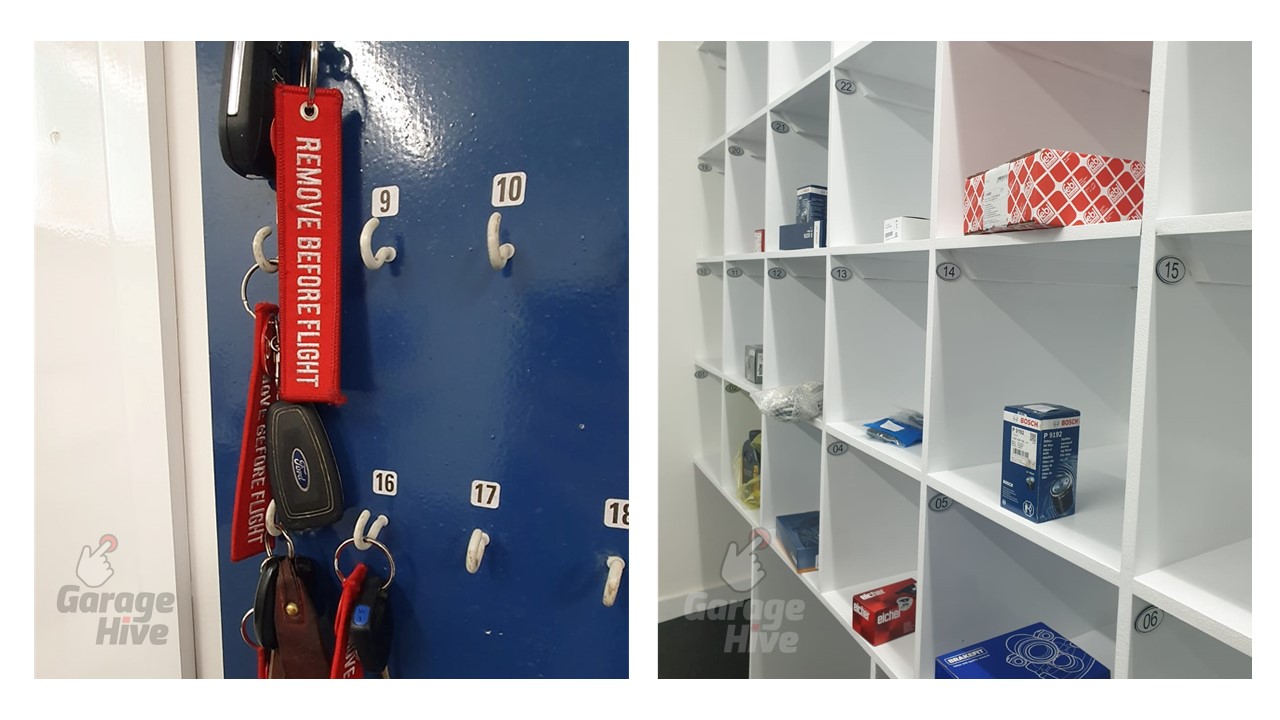
Let’s see what the employee-vehicle journey looks like when making these small changes:
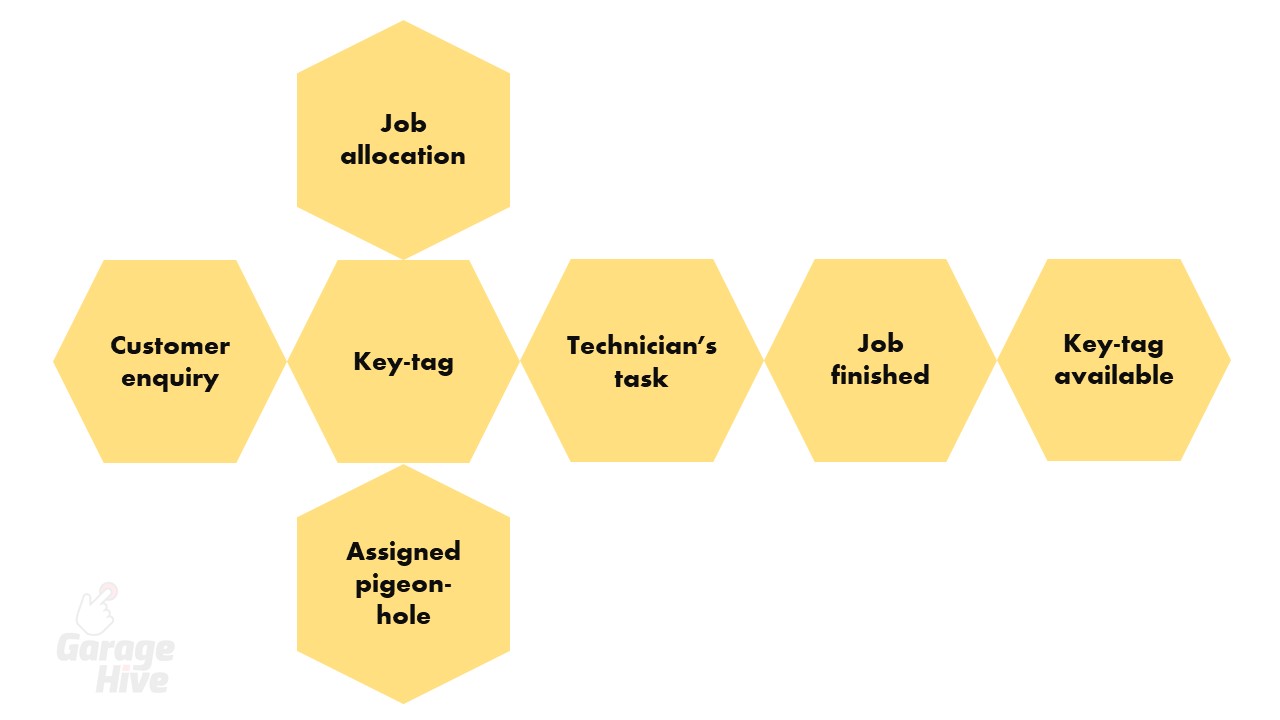
- A client books a service that may require parts to be ordered.
- If the parts arrive before the vehicle, you need to pre-assign the jobsheet with a reference number that is available as both a numbered pigeon-hole and a corresponding key-tag. Place all parts into the relevant pigeon-hole.
- Once the vehicle arrives, use the same key-tag to put on the customer’s keys. This reference number will remain the same for the jobsheet, key-tag and pigeon-hole until the job is finished. In the scenario where the vehicle arrives first, you can designate a key-tag first. Any parts that come later can then be put into the assigned pigeon-hole.
- The manager can then allocate these jobs to the appropriate technicians; they will check what their tasks for the day are and then pick up the correct keys and the right parts from the designated pigeon-hole without wasting any time.
It is essential to book incoming stock in as soon as it arrives as this will ease the process of invoicing to customers. Garage Hive will help you track your stock and recognises the specific parts that are allocated to particular jobs.
You can specify a person responsible for this each day or make sure everyone books in their parts as soon as they arrive.
Also, remember to take the key-tag off the client’s keys after the job is finished. It is easy to forget, don’t lose them! We suggest keeping the available ones in a separate box somewhere close to your front counter.
If done correctly, your workshop should run smoother and will be more organised. It will be easier to indicate if you can start a job or if you are still waiting for stock to arrive. Your technicians will be less frustrated and more productive. On top of that, your accountant will thank you too.
Let us know how you are keeping your business organised!
Copy link